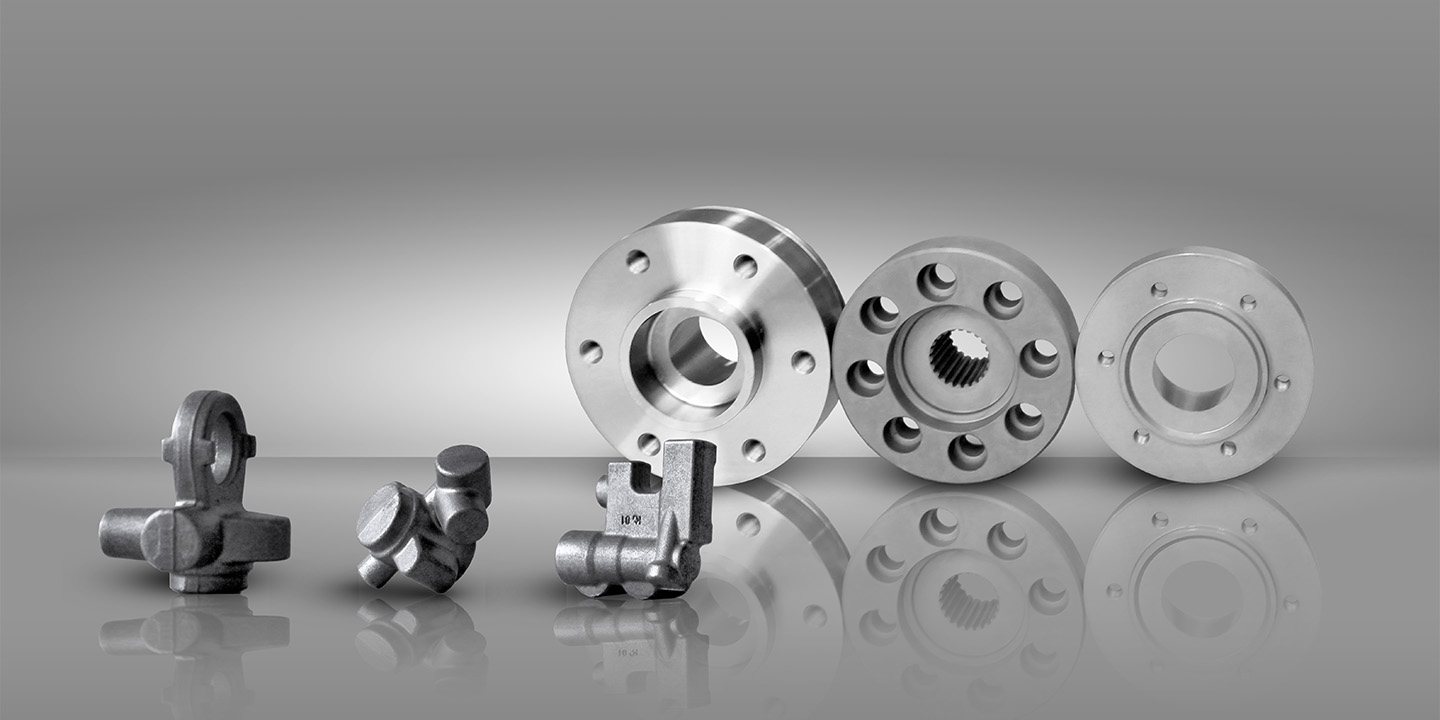
What do we produce?
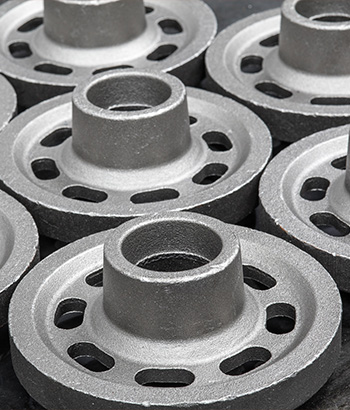
Forgings
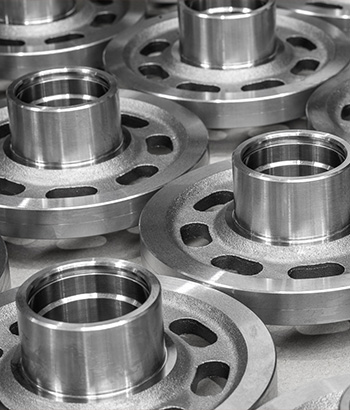
Semi-machined parts
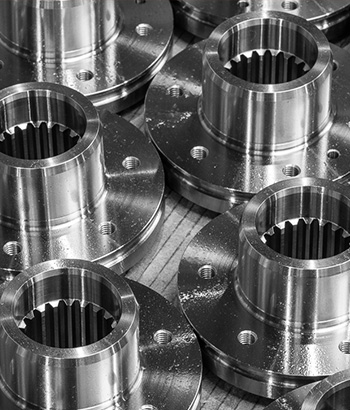
Machined parts
Production Divisions
The process of forging and finishing
The basic technology in the production of forgings, made at Kuźnia Polska, is the hot forging of die forgings weighing up to 25 kilograms using forging presses, crank presses with Direct Drive System, forging automatic – Transfer, air hammers and upsetting machines.
1
Steel warehouse
We use high quality carbon, alloy, stainless steel in over 100 grades storing them onto the area of 4000 m2.
2
Heating and cutting room
Heating of sheared pieces of steel, called charges, to temperature of 1,200˚ C in electric induction furnaces or gas-fired furnaces and their subsequent forming of the required element in a die.
3
Forging
In the forging of forging-crank-operated forging presses of 10 to 25 MN pressure, air hammers with a striking forth (hit energy) between 1,600 to 10,000 KGm and vertical and horizontal forging machines with 2 to 12 MN pressure are used. It is also possible to manufacture small mass forgings – i.e. from as little as 0.25 kilograms using PS-type screw presses.
4
Trimming
Removal of excess material in the form of fins – this is a dubbed trimming operation on crank or eccentric presses. During this stage of the production process aperture swaging, bending and calibrating is performed.
5
Heat treatment
Heat treatment of the forgings aimed at giving the forging high strength. In carbon and alloy steel forgings heat treatment in the form of quenching and tempering (quenching in water, oil or polymers), normalizing or isothermal annealing is used. Strength is also attained through a controlled cooling after forging.
6
Shot blasting
Shot blasting operation – cleansing of the forging’s surface of so-called scales (hard surface bloom resulting from steel oxidation at high temperatures). This operation takes place on special machines called shot blasters, which use steel pellets of great hardness and with a shot diameter ranging from 0.8 to 1.2 mm.
7
Calibration
Finishing operations including cold calibration, straightening, marking, grinding and burnishing.
8
Visual inspection
Meticulous visual inspection of each item in order to ensure 100% faultless forgings: with underfills, joggles, scale pitting, cold shuts.
9
Final control
Final control aimed at statistical checking of the quality of manufactured forgings and to provide a quality warranty through quality certification in accordance with the client’s requirements.
Our machines state
Model | Quantity | Description |
---|---|---|
HASENCLEVER 2500 | 2 | Crank press with forming force of 25 MN |
SMERAL LZK2500 | 3 | Crank press with forming force of 25 MN |
FICEP DD190 DIRECT DRIVE | 1 | Screw press, nominal power of 331 kJ and forming force of 24 MN |
HASENCLEVER | 2 | Crank press with forming force of 16MN |
DREHER | 1 | Crank press with forming force of 16MN equipped in TRANSFER |
SMERAL LMZ1600 | 3 | Crank press with forming force of 16MN |
SMERAL LZK1000 | 3 | Crank press with forming force of 10MN |
HASENCLEVER | Few smaller presses with forming force of 5 MN, screw presses with screw diameter of 180 mm and few hammers – 3000 kg ( hit energy 10 000 KGm ), 2000 kg, 1000 kg, 500 kg. | |
OLIVOTTO | Automatic heat treatment line – set up for 2008 | |
LLR1000 | Press | |
KARL DEUTSCH UHW750/1,2, UH60 | MPI units |
Machining
In order to meet Customers’ expectations, Kuźnia Polska S.A. has broadened its range of ready-made machined products. At present our stock of machining tools includes vertical machining CNC centers, CNC lathes with powered tools, which also perform drilling and threading, vertical and horizontal milling machines, turning lathes, drillers, relieving lathes and hydraulic presses. We produce mainly ready-made elements such as levers, flanges and towing hooks. Any process engineer, who designs the process, must also take into account a number of important parameters, which cover both the technological possibilities of the forging element (in other words giving it the desired shape) and the functional qualities, that the client stipulates, such as hardness, resistance, hardenability, structure etc.
1
Clamping devices
2
Machines
3
Hall
The Machinery:
Machine tool | Maximum dimension of worked piece (mm) | Maximum weight of worked piece (kg) |
---|---|---|
Machining centre – MAS QUICK 500 | 500 x 500 x 400 | 300 |
Machining centre – BROTHER TCR2B | 400 x 300 x 300 | 120 |
Machining centre – Okuma MA 400 | 600 x 500 x 500 | 300 |
Machining centre – MAZAK VTC 200C | 1600 x 500 x 500 | 650 |
Machining centre – 4940 YCM H400B | 500 x 500 x 600 | 500 |
Machining centre – Okuma Multus B300 | Æ 250 x 700 | 150 |
Machining centre – Okuma Multus U4000 | Æ 600 x 1500 | 150 |
Machining centre – Miyano ABX-64SYY2 | Æ 165 x 125 | 20 |
Lathe – Okuma ES L8M | Æ 200 x 500 | 50 |
Lathe – Okuma GENOS L250 | Æ 200 x 500 | 50 |
Lathe – Okuma GENOS L300M | Æ 300 x 450 | 100 |
Lathe – Okuma GENOS L400 | Æ 300 x 500 | 100 |
Grinder CNC – OKAMOTO OGM250UEX III | Æ 200 x 500 | 20 |
The basic premise of our strategy is to offer the product that is processed to a maximum degree. Currently it is approximately 25%.
We use:
- machining (including pull broach)
- zinc-nickel coating
- phosphating
- KTL protection
- nitriding
We also offer only machining services without the forging process for some of our products.
Our strategy: to be a supplier of components for assembly lines.
Tooling Room
Kuźnia Polska disposes its own Tooling Room, serious modernized in 2005 being self-made toolmaker, ensuring the production processes so flexible as possible and offering very professional service outside. Continuously upgraded machines and IT systems are able to keep the highest market needs. Designing, engineering and programming of CNC centres are performed onto the advanced CAD/CAM positions. The leading software is CATIA.
We guarantee especially:
- heat treatment of the tools and nitriding of the cavity surface in vacuum furnace
- hardening of the tool steels and derivatives in vacuum furnace
- 3-axle machining of the products in dimensions 2000mm x 1400mm x 700mm
- 5-axle machining of the products in dimensions D=1100mm h=700mm
- CNC lathe machining D=390mm L=500mm
- electroerosion machining of the products in dimensions 650mm x 450mm x 350mm
- electroerosion wire machining of the product in dimensions 500mm x 350mm x 200mm
- programming of CNC tool machine – 2, 3, 5-axles
Among other thinks, we have:
- catalytic nitriding furnace
- WCL hardening work cell and derivatives in a protect atmosphere
- WNC, WNLV hardening work cell and derivatives
- heating furnace with carrying capacity of 3,5 tons
Our products
Forgings to passenger cars and trucks
75% of the forgings produced by Kuźnia Polska, are dedicated to multiserial and repeatable manufacturing to automotive and truck branch.
Forgings to machines and agriculture industry
15% of the forgings and machined parts work in special agricultural vehicles like tractors, harvesters and agro-equipment.
Forgings to machine industry
5% is different parts to modern engines, transmissions and road devices.
Forgings to energy and railway
3% of our assortments supply the renewable energy and railway sector.
Forgings to air force
2% of the production is advanced technology fortified by the highest quality demands for air force industry.
Call our company:
+48 (33) 85 48 283
+48 (33) 85 85 111